Our Mission
Reinventing how we recycle plastics, for a more sustainable future.
The world has a waste problem. How we recycle it needs to change.
To create the sustainable and circular economy we need, rapid development of transformational technologies is needed. ReVentas is meeting this challenge, taking the most common waste plastics found in the world today, and returning them into the products the world needs tomorrow.
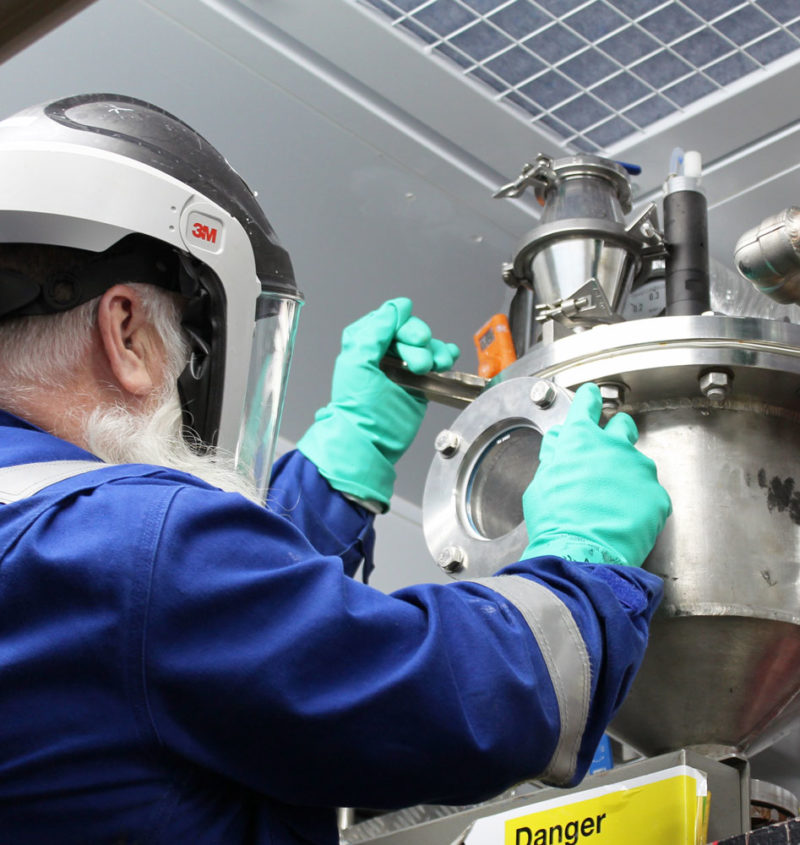
A Novel Dissolution Recycling Technology
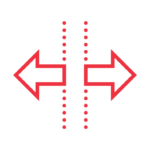
01.
Feedstock Preparation
The post consumer feedstock is prepared through shredding and granulation ready for dissolution, with any large non-polymer contaminants removed.
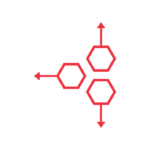
02.
Polymer Dissolution
The polymer is fed into our dissolution vessel, which rapidly dissolves the target polymers forming a liquid slurry which is ready for filtration.

03.
Filtration
The polymer-solvent slurry is then passed through a series of filters removing any solid particulates and any dissolved contaminants such as odours, VOCs and chemicals present in the feedstock.
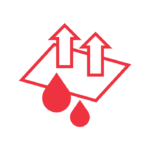
04.
Polymer Separation
The polymer in the now clean slurry is separated from the solvent, allowing the polymer to be recovered and the solvent to be reused in the process.

05.
Drying Extrusion
A final drying step is now applied to the polymer before the polymer is then stabilised and then extruded to form pellets ready for use in new applications.
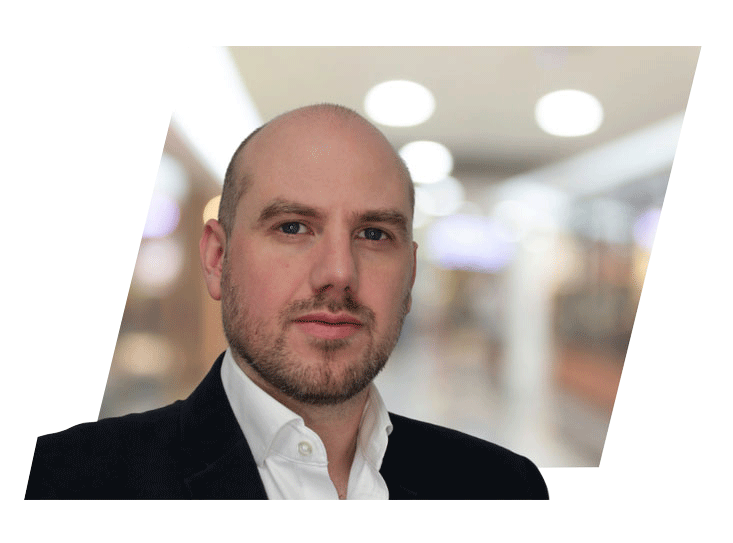
“ReVentas is enabling a future where waste is no longer something to throw away but is a valuable resource to be harnessed, creating the products we need tomorrow.”
Tom Rose, CEO
ReVentas material can displace virgin plastics across multiple industries.
Supported By
Working for ReVentas
If you are looking for that pivotal change or new start in your career, you are looking in the right place. ReVentas is at the forefront of knocking through barriers, particularly when it comes to supporting the circular economy. Keep an eye out for open vacancies below.
Get in Touch
Impact Technology Centre,
1 Fraser Road, Livingston, EH54 7BU
+44 (0) 131 370 1600 / hello@reventas.co.uk